In industrial refrigeration, the efficiency and longevity of systems heavily depend on the removal of non-condensable gases. An ammonia auto purger plays a crucial role in this context, maintaining the purity of the refrigerant by automatically purging air and other non-condensables. These units are vital for the operational efficiency of large-scale refrigeration systems commonly found in food processing plants and cold storage facilities. Keep reading to delve deeper into how ammonia auto purgers function and the myriad of benefits they offer.
Understanding the Function of an Ammonia Auto Purger in Refrigeration Systems
An ammonia auto purger is essential for removing non-condensable gases like air from refrigeration systems, which can reduce efficiency and increase energy use. By automatically detecting and expelling these gases, it ensures ammonia circulates freely, improving heat transfer and overall system performance.
This automation reduces the need for manual monitoring, making operations smoother in industries like cold storage. Additionally, by keeping the system clean, the ammonia auto purger helps lower ammonia charge levels, minimizing leak risks and supporting eco-friendly refrigeration.
The Mechanics Behind Ammonia Auto Purgers: Enhancing System Efficiency
An ammonia auto purger is an efficient system that differentiates between ammonia and undesired gases using differential condensation. It uses the varying condensing points of ammonia and other gases to achieve precise separation, maintaining refrigeration system efficiency. The purger operates by intermittently taking small amounts of gas from high points of the refrigerant circuit, which are then passed through a condenser.
Ammonia condenses at higher pressure than air, making it easily liquefied and returned to the system. The process is managed by a sophisticated control system that regulates the purging interval based on system pressure, temperature, and other critical parameters. This ensures uninterrupted service in industrial applications and eliminates the need for manual purging, transforming the process into a streamlined and cost-effective operation.
The Impact of Ammonia Auto Purger on System Performance and Cost Savings
An ammonia auto purger not only improves the performance of a refrigeration system but also offers significant cost savings. By eliminating non-condensable gases, the compressor’s work is less, resulting in reduced energy consumption and lower utility bills. Additionally, maintenance costs decrease due to less strain on the compressor and other components, resulting in longer equipment life and fewer repair or replacement expenses.
The reduced need for manual purging also reduces disruptions and labor costs associated with maintenance routines. Accurate functioning of an ammonia auto purger mitigates risks associated with non-condensable gases, ensuring safety and reliability in industrial settings. A well-maintained system with minimal leaks reduces the risk of penalties and losses due to environmental regulations, contributing to sustainable cost savings.
Navigating the Installation and Maintenance of Ammonia Auto Purgers
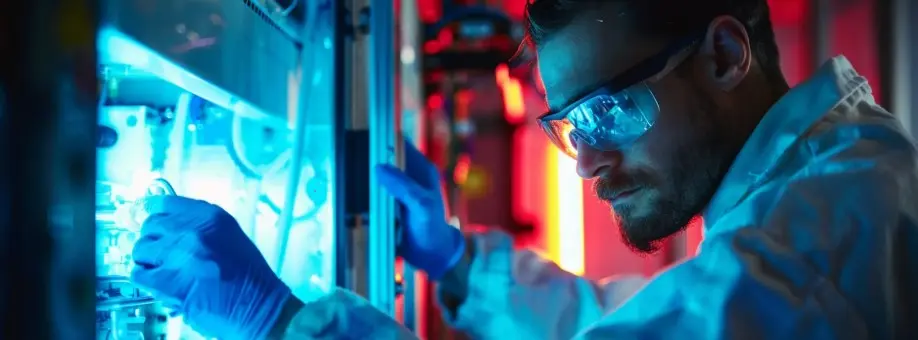
The installation of an ammonia auto purger is crucial for a refrigeration system’s design and the facility’s specific needs. It should be strategically integrated to trap and remove non-condensable gases, and professional installation is recommended. Regular maintenance involves checks for leaks, control settings, and condenser function, ensuring the purger’s longevity and efficiency.
Operators should be trained in understanding the purger’s signals and outputs to identify system issues and take corrective measures. Proper documentation and logs of purger operations are also essential for standard maintenance protocol. This data can help identify patterns, forecast maintenance needs, and facilitate troubleshooting if issues arise within the refrigeration system.
Real-life Applications and Case Studies: The Effectiveness of Ammonia Auto Purgers
Ammonia auto purgers offer practical benefits in various industries, including cold storage, food processing, beverage, and chemical industries. They help maintain optimal temperatures, reduce energy costs, and improve operational effectiveness. In cold storage facilities, they help operators meet storage requirements while minimizing concerns over fluctuating ammonia levels and non-condensable gases. In food processing, auto purgers reduce energy costs, product loss, and energy consumption, leading to extended shelf life and reduced energy consumption.
Breweries benefit from consistent refrigeration for product quality, while auto purgers improve production consistency, energy management, and operational efficiency. The chemical industry, which often requires critical storage temperatures for various compounds, benefits from the precision offered by ammonia auto purgers, meeting stringent refrigeration requirements and safeguarding chemical properties and integrity.
Overall, the integration of ammonia auto purgers into industrial refrigeration systems offers measurable improvements in efficiency, cost savings, and reliability. With proper installation and maintenance, these devices ensure that refrigeration systems operate at peak efficiency, ultimately supporting the sustainability and productivity goals of modern industry.